When designing electronics enclosures for naval applications, survivability under extreme mechanical shock is not optional—it’s essential. MIL-DTL-901E, formerly known as MIL-STD-901D, is the defining standard for shock qualification of shipboard equipment. This standard governs how enclosures and their mounted electronics must perform when subjected to the violent shock loads that occur during combat or hazardous operations at sea.
Electromet specializes in rugged, shock-qualified enclosures that meet or exceed the stringent requirements of MIL-DTL-901E. In this article, we unpack what the standard entails, the technical challenges it poses, and how Electromet solves them through precise engineering, materials selection, and validated design.
What Is MIL-DTL-901E?
MIL-DTL-901E is a U.S. Navy detail specification used to qualify equipment for survivability under high-impact shock. It applies to equipment mounted on ships and submarines where failure during shock events could compromise the mission or endanger personnel.
The standard is structured to account for:
- Grade A vs. Grade B equipment: Grade A equipment is essential to the safety and combat capability of the ship; Grade B is non-critical but still mission-relevant.
- Lightweight, medium weight, and heavyweight equipment: Categorized by mass and center of gravity.
- Shock test types: Including lightweight hammer blows, medium weight drop tests, and heavyweight barge explosions.
Each piece of equipment must undergo appropriate test types based on its mass, configuration, and shipboard mounting orientation.
Barge Testing: The Ultimate Proof Point
For heavyweight, critical (Grade A) equipment—such as large electronics racks and power enclosures—the MIL-DTL-901E barge test is the most demanding assessment.
In this test:
- Equipment is mounted to a floating barge deck in its operational orientation
- Underwater charges of 60 pounds of HBX-1 explosive are detonated at various standoff distances
- Equipment must remain attached and operational after multiple shocks (typically 4–6 detonations)
Pass/fail criteria include:
- Structural integrity of the enclosure (no deformation or collapse)
- Functional performance of internal systems
- Retention of mounting integrity (hardware must remain secure)
Electromet’s enclosures are engineered specifically with this test in mind.
Engineering for Shock Resilience
Surviving the barge test requires enclosures to manage extremely high accelerative forces (100g+ instantaneous). Electromet addresses this through:
- Finite Element Analysis (FEA) to simulate stress propagation through the enclosure during shock events. This informs material thickness, weld placement, and brace geometry.
- High-strength materials such as cold-rolled steel, 5052/6061-T6 aluminum, and internal reinforcement frames.
- Redundant load paths that distribute shock energy across multiple structural members.
- Floating subframes or shock tray systems for internal PCBs and mission electronics.
Our engineers treat each enclosure as a dynamic structure—one that must deform strategically without failing.
Mounting Strategies and Isolation Systems
Shock energy is only partially absorbed by the structure; the remainder transmits to mounting surfaces. That’s why MIL-DTL-901E testing also focuses on how enclosures are attached to shipboard infrastructure.
Electromet designs and tests:
- Bulkhead-mounted and deck-mounted configurations
- Custom shock isolation platforms using tuned elastomers or mechanical mounts
- Reinforced interface points to minimize stress risers
We often perform dual-mode mounting analysis to confirm compliance in both fore-aft and athwartship orientations.
Collaboration Between Electromet and IDC Engineers
Achieving reliable MIL-DTL-901E shock qualification requires more than just enclosure strength—it demands a fully integrated system that can absorb, isolate, and redirect impact energy across multiple axes. That’s why Electromet partners closely with a Jonathan Group company specializing in high-performance vibration and shock isolation solutions for defense applications.
IDC’s wire rope isolators and engineered mounting platforms are routinely incorporated into Electromet enclosures to deliver multi-axis energy mitigation for naval systems. Whether protecting rack-mounted electronics from hull-borne shock or isolating mission-critical C4ISR equipment from structural resonance, our collaboration ensures that mechanical protection is engineered from the inside out.
Together, Electromet and IDC offer:
- Fully shock-qualified enclosures with embedded isolation
- Tuned isolator assemblies for deck-mounted and bulkhead-mounted systems
- Custom validation via thermal, vibration, and drop testing
- Complete documentation and traceability for naval compliance
Certification and Traceability
Compliance with MIL-DTL-901E isn’t just about surviving a test. Programs demand full documentation and traceability.
Electromet provides:
- Test reports from accredited facilities
- Drawings with revision control
- Material certs and fabrication traceability per MIL-Q-9858 or ISO 9001
- Weld and fastener inspection reports
Our process ensures that field units match qualification articles—critical for programs under NAVSEA, SPAWAR, or DLA oversight.
A Platform-Agnostic Solution
Electromet’s MIL-DTL-901E enclosures are deployed aboard:
- Aegis-class destroyers
- Amphibious assault ships
- Littoral combat ships (LCS)
- Subsurface command and control stations
Each application has its own vibration, shock, and EMI environment—but 901E compliance is a consistent baseline for survivability.
Beyond Compliance: Designing for Longevity
Whereas MIL-DTL-901E ensures a moment of survivability, Electromet’s design ethos ensures long-term durability. That means:
- Coatings that resist corrosion and electrolysis
- Ingress protection (IP65+) against salt fog and washdown
- Thermal considerations for internal electronics post-shock
This holistic approach transforms a compliant box into a mission-ready platform.
MIL-DTL-901E is more than a checkbox—it’s a gatekeeper for naval electronics reliability. Electromet’s shock-qualified enclosures are designed from the inside out to meet this challenge.
Whether you’re upgrading legacy systems or designing next-gen platforms, our team can deliver enclosures that are tested, certified, and built to survive the fight.
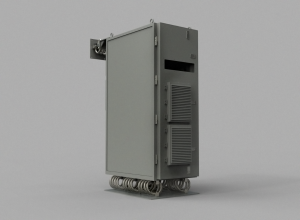
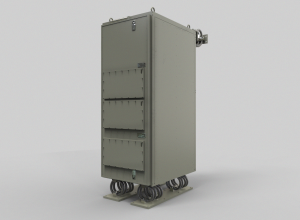