MIL-STD-810F is a test method standard established by the U.S. Department of Defense to define a series of laboratory test conditions that simulate the environmental stresses systems will encounter in field use. Originally published in 1962 and continuously updated, the “F” revision was released in 2000 and has remained a widely used and referenced version within the defense and rugged electronics industries.
MIL-STD-810F outlines procedures to ensure materials, components, and complete systems are qualified to perform in extreme operational environments. It is not a product specification, but a guide for tailoring test conditions to mirror the actual field environment of use. The intent is to reduce failures, increase mission reliability, and inform design tradeoffs through environmental realism.
This blog offers a technical breakdown of MIL-STD-810F, explaining its structure, methodologies, and how engineers use it to qualify rugged enclosures, 19″ EIA racks, and defense electronics.
Structure of MIL-STD-810F
MIL-STD-810F is divided into three major parts:
Part 1: General Program Guidelines
Defines the environmental engineering program, including tailoring methodology and program documentation requirements.
Part 2: Laboratory Test Methods
Lists 24 distinct test procedures addressing a wide range of environmental conditions.
Part 3: Appendices
Provides supporting material such as design guidelines, risk assessments, and environmental stress profiles.
Unlike many MIL-STDs, 810F requires test programs to be tailored, meaning each test must be selected, modified, and justified based on the system’s mission profile, deployment region, and lifecycle exposure.
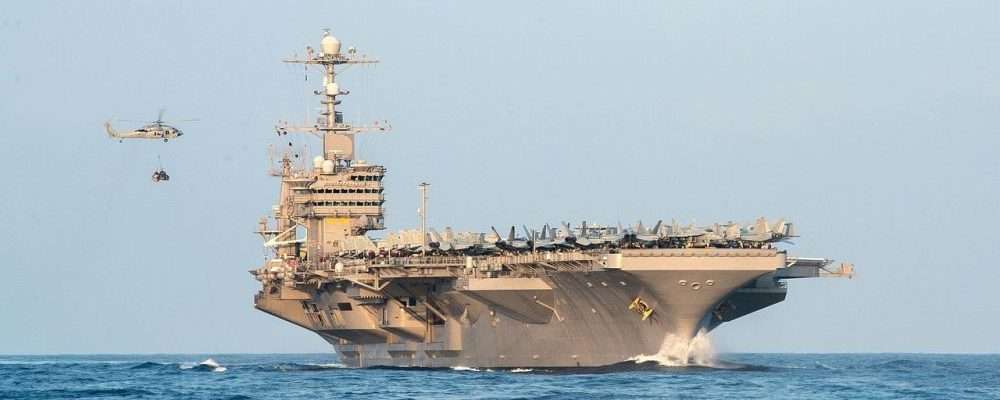
Key Environmental Test Methods
MIL-STD-810F contains 24 test methods. While not every method applies to every system, several are highly relevant for enclosure and electronics packaging engineering.
Method 501.4 – High Temperature
- Simulates operation and storage in elevated ambient temperatures (e.g., desert or engine room conditions).
- Tests thermal endurance, material stability, and internal cooling effectiveness.
- Typical ranges: +50°C to +71°C (operating); +85°C (storage).
Method 502.4 – Low Temperature
- Simulates exposure to extreme cold (e.g., arctic or high-altitude conditions).
- Assesses seal flexibility, material embrittlement, and thermal cycling effects.
- Typical ranges: -20°C to -57°C, tailored per deployment.
Method 507.4 – Humidity
- Evaluates susceptibility to moisture absorption, corrosion, and electrical leakage.
- Typically conducted over 10–15 days in 95% relative humidity at 30–60°C.
- Ensures materials don’t support fungal growth or delaminate.
Method 509.4 – Salt Fog
- Replicates marine and coastal conditions.
- Exposes equipment to a 5% NaCl aerosol for 48–96 hours.
- Assesses corrosion resistance of coatings, fasteners, and electrical contacts.
Method 510.4 – Sand and Dust
- Tests particle ingress and abrasion in desert or open-deck deployments.
- Blasts fine or coarse particles at 1.5–29 m/s at 23–65°C.
- Evaluates IP rating integrity, filter performance, and moving parts endurance.
Method 514.5 – Vibration
- Subject to detailed tailoring based on transportation mode (ship, air, wheeled vehicle).
- Includes broadband random, swept sine, and shock profiles.
- Frequencies and amplitudes range from 5 Hz to 2000 Hz.
Method 516.5 – Shock
- Measures survivability during impact events: handling drops, crash loads, weapon shock.
- Includes functional shock, transit drop, and crash hazard procedures.
- Often used in conjunction with MIL-DTL-901E and MIL-STD-167-1A.
Other Relevant Methods Include:
- Method 503.4: Temperature Shock
- Method 506.4: Rain / Drip Resistance
- Method 511.4: Explosive Atmosphere
- Method 528.1: Roller Drop / Rail Impact
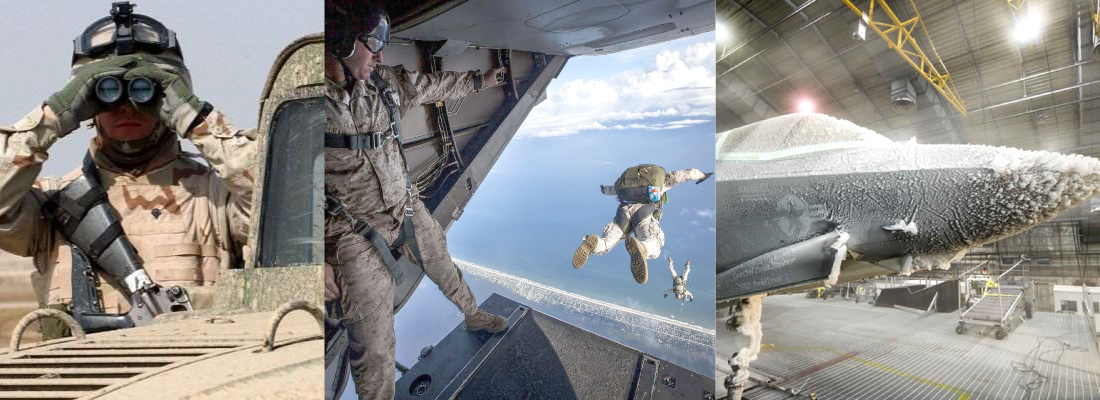
Tailoring and Test Planning
A key principle in MIL-STD-810F is the notion of test tailoring. Rather than blindly applying all methods, engineers are required to:
- Define the mission and environmental profile of the system
- Identify operational and non-operational conditions
- Select applicable methods and adjust parameters (e.g., temperature extremes, durations)
- Justify tailoring decisions in a test plan
Tailoring often uses data from:
- Geographic deployment maps (temperature/humidity norms)
- Vehicle vibration spectra
- MIL-HDBK-310 or DEF STAN climate data
Common Misconceptions
- MIL-STD-810F isn’t a checklist. Systems aren’t “810F certified”—only tailored test plans validated by data.
- Passing a lab test ≠ field success. It only means the system survived one exposure condition under defined constraints.
- MIL-STD-810G isn’t a replacement. While newer revisions exist (e.g., 810G, 810H), 810F remains the contractual baseline for many legacy programs.
Engineering Implications for Enclosures
For rugged enclosures, racks, and assemblies, 810F drives numerous design decisions:
- Sealing and IP Ratings: Driven by Methods 507 (Humidity), 510 (Dust), 506 (Rain)
- Material and Finish Selection: Driven by Method 509 (Salt Fog), corrosion index
- Shock Mounting Systems: Driven by Method 516 and other shock-related MIL-STDs
- Thermal Design: Dictated by Methods 501/502 for passive/active cooling validation
Summary
MIL-STD-810F is a flexible yet rigorous framework for validating equipment under real-world environmental conditions. It does not guarantee field survivability—but it greatly increases confidence that systems will perform when deployed.
For engineers tasked with specifying, designing, or testing rugged enclosures, understanding the nuances of MIL-STD-810F is essential. Tailored application of its methods leads to smarter materials, better systems integration, and fewer failures in the field.
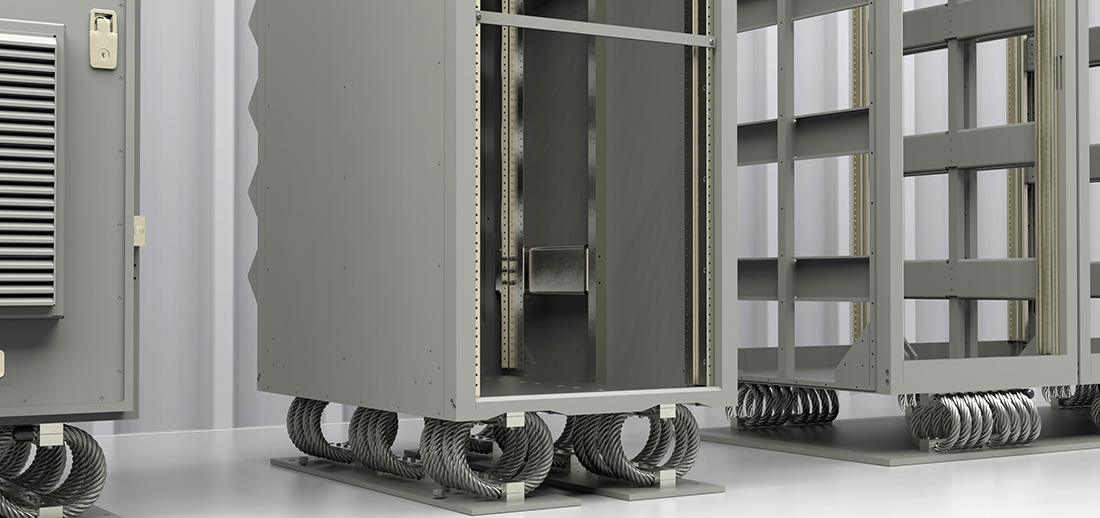